Table of Contents
Have you ever noticed how complicated things become simple after someone explains them properly? We know how challenging it may be to process material. So many complementary nuances are involved that some professional assistance may come in handy.
We updated our guide about aluminum CNC machining, so it is completely up-to-date for 2022. Read below to discover types of aluminum, cutting tools to machine it, and common manufacturing operations.
1. Why Machining Aluminum Can Be Challenging?
Aluminum is the most affordable and popular metal. It has various applications due to several ways to process workpieces made of such material. However, machining aluminum is fairly challenging. The scary part is that this metal is soft by nature and has low melting temperatures.
The extent of problems detailed further may vary. It depends on the aluminum alloy used. You may face difficulty cutting aluminum, especially thin sheet layers of the metal. It is associated with the heat of friction, which frequently exceeds the melting point of aluminum.
Additionally, the hardness of the metal is low, and the use of harsh cutting tolling may wrinkle or stretch the entire workpiece.
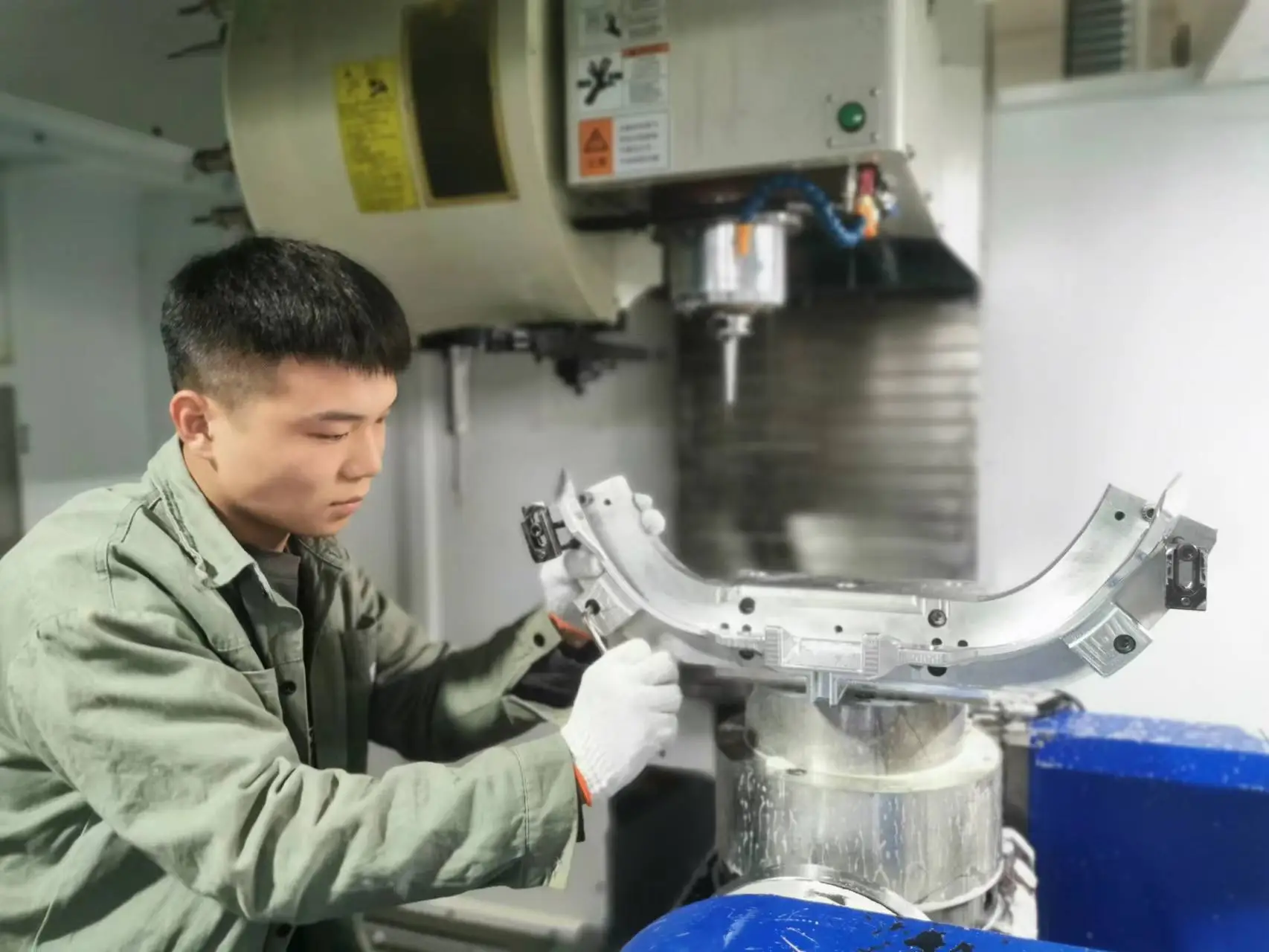
2. Common Types of Aluminum
There are several common types of aluminum as the material for fabrication. Additionally, it is possible to distinguish 7 grades of aluminum alloys.
1. 2024-T351 aluminum. It is the hardest aluminum, mostly used in aircraft. It is also known for the difficulty of its machining, as it requires specialized tooling and particular manufacturing settings.
2. Aluminum alloy foil. In contrast, it is the most flexible aluminum, which can be processed with a limited range of machining options.
3. Sheet aluminum. It is rather the form of manufactured aluminum workpieces. By hammering, stamping, or spinning, sheet layers of the metal can be obtained. In the process, types of aluminum may be combined to obtain extra properties.
4. Clad aluminum. You may have heard of it as treated aluminum. It has a coating of any type, such as zinc, silicon, nickel, or magnesium. Treated aluminum is durable and enhanced with extra properties due to coating.
5. Pure/Bare aluminum. As evident from its name, it is pure unprocessed metal. Typically, it is needed for further use in the manufacturing process. It is rarely used as a material for workpiece preparation and further components manufacturing. It is explained by the lack of corrosion resistance and low durability.
6. Aluminum Alloys. Finally, there are 8 grades (series) of aluminum. Each of them has distinct properties and its own unique areas of applications.
- 1000 series is 99% aluminum.
- 2000 series is aluminum alloy with copper.
- 3000 series is aluminum alloy with manganese.
- 4000 series is aluminum alloy with silicon.
- 5000 series is aluminum alloy with magnesium.>
- 6000 series is aluminum alloy with magnesium and silicon.
- 7000 series is aluminum alloy with.
For more information on aluminum, you can also check here.
3. Cutting Tools for Aluminum
Here’s the secret: CNC tooling for aluminum cutting is more than just a few pieces of metal that is hard enough. We detailed below the most frequently used types of tools and some distinctive features they have in common.
The crucial point is that you absolutely should not use any of the cutting tools that are intended for general purposes. As per the reasons detailed above, aluminum is different from other metals. So, the listed tools are to be purchased only if a supplier specifies their suitability for aluminum.
- Drill bits for small spot cutting.
- End mills for cutting material straight down without a pre-drilled hole or spot.
- Face mills for flat section machining.
- Reamers for widening already created holes.
- Gear cutters for simply making various types of gear.
- Hollow mills for enclosing and revolving around a cylindrical workpiece, creating pre-thread diameter effectively.
- Thread mills for simply cutting external and internal threads.
- Slab mills exploit quick wide and narrow cuts to create flat surfaces.
Fly cutters exploit broad and shallow cuts to produce a smooth surface finish.
Common Types of Cutting Tools:
Cutting Tool Material
You may be offered, by a supplier, one of the common cutting tool materials.
- Carbon tool steel
- High-speed steel
- Ceramics tool
- Cemented carbide
- Cubic boron nitride
- Diamond
It is a detailed aspect that defines what a particular material a cutting tool is made of will suit your purposes better.
But typically, aluminum requires softer but sharper tooling than stainless steel. It is because of the aluminum’s softness.
Among the ones listed above, carbide responds to the requirements better than others. It is also an affordable material for tooling.
Flutes
In CNC machining, flutes are not musical instruments but rather sharp slots positioned along with a cutting tool. They do the cutting work when a bit is spinning.
In CNC machining of aluminum, cutting tools, especially ones made of carbide, with 3 flutes are the gold standard. Such a number of sharp slots offers the balance of tool strength and chip clearance, which is detailed further in the text multiple times.
In case you need to reduce the probability of tool constipation with metal chips even more, you may choose 2 fluted cutting tools. You will see how it works for a particular type of aluminum; perhaps, it is your best choice.
You rarely need a cutting tool with more than three flutes (a range of options may include even 8-flutes tooling). Aluminum is a soft metal, and cutting force is not crucial for such material.
Helix Angle
The Helix angle is the angle between the axial line of a bit and any of its sharp slots. You can see examples of helix angles in the infographics below.
The helix angle controls the angle at which the cutting edge enters a manufactured component when a cutting tool is rotating.
The simple dependency is the larger the helix angle, the more grade entry of the flute of tooling. Angles enable the smoothness of the transaction and, as a result, to achieve the desired depth of cut.
As a rule of thumb, a higher helix offers a better surface finish but produces more heat. Considering that aluminum is a metal with a low melting point, choosing an appropriate helix angle is crucial.
Typically, we recommend a 35-degree helix angle for roughing. 45-degree helix angle for finishing. 40-degree helix angle for other purposes, or as a viable replacement of alternative helix angle options.
Other Worthwhile Features
We highly recommend you pay close attention to cutting tools polishing. Even the most advanced and expensive tooling tends to deteriorate in sharpness over time. So, if you do not want your tools to become dull, polish their flutes regularly.
Do not use uncoated tooling. Yes, they are more affordable and still fantastic. You may consider uncoated tooling when unsure what coating suits your purposes and tools better.
Still, it is recommended that you use tooling with ZrN or TiB2 coating (explained further in the text).
4. Feeds and Speeds
Here is the thing. It doesn’t matter if your tooling is appropriately chosen if the settings of a CNC machine are not suitable. Typically, wrong feed and speed rates ruin the entire machining process by deteriorating both material and tooling.
Speed Rates
Speed rate is the first variable in CNC machining to discuss. It is calculated according to specific formulas detailed below.
Speed (RPM) = (SFM x 3.82) / D
Where: SFM is Surface Feet per minute; D is tool diameter.
Speed (spindle speed or RPM) is the number of rev/min or turns of a cutting tool. It defines how fast a tool would be cutting chips of material.
Feed Rates
Feed rate is the second major variable in CNC machining. The formulas for it are the following:
Feed (Inches per minute or IPM) = RPM x FPT x Z
Where: FPT is Feed per Tooth; Z is the number of teeth in a cutting tool.
Feed rates define the distance or depth a cutting tool deepens into a workpiece during one spindle revolution.
As a bonus, we attached the infographics below, showing the feed rate multiplier.
5. Common Operations for Machining Aluminum
Facing
In other words, it is smoothing a plane surface at right angles. It also means polishing inserts of a part.
Typically, the material is removed from the end and shoulder or a workpiece. Lathe and milling machines are CNC centers that employ this manufacturing technique.
Pocketing
Pocketing operation is needed when removing the material with a closed boundary down to a depth required.
The technique requires flat bottom-end mills. First, roughing operations are performed to remove excessive material. Then, a more precise end mill (finish end mill) polishes the pocket.
Slotting
When you perform shaping (another name for slotting), a workpiece is fixed on the machine table and is fed to a single-point cutting tool.
Typically, you need a stub flute endmill or trochoidal milling & chatter to cut deep, precise slots.
Slotting is often used to cut external shapes and intricate forms.
Drilling
It is the most straightforward operation possible. Drilling is the process of cutting holes (or circular cross-sections if you like) in a material, by using a rotating cutting tool.
A drill bit is used to cut a new hole or enlarge an old one (although there are other operations for holes enlarging as well). The bit is pressed against a workpiece in a linear direction.
Tapping
Last, tapping is a machining process for creating internal threads.
A tap, which has given the name for the entire operation, is a cylindrical or conical thread-cutting tool. It has many threads of required form on the periphery. By combining rotary with axial motions, a thread can be cut even in such a soft material as aluminum is.
Tapping is needed to create a thread inside a hole to accommodate a cap screw or bolt further.
6. Best Strategies and Tips for Aluminum Machining
To assist you in CNC aluminum machining, we accumulated our experience and formed a list of strategies, advice, and tips.
- Maintain a consistent temperature. Fluctuations in working environment temperature may cause an excess in humidity, which causes aluminum oxidation. Alternatively, failure to maintain a stable temperature of the part while machining would immediately result in batches of sub-quality production with no further use. So, always consult specifications and suppliers of metal to know that temperature is to be maintained.
- Clean metal chips. Sure, dust collector systems may assist in eliminating sticky aluminum ships. But, it is essential to clean the machine on and off manually. You may run a coolant mist through the machine to reduce the stickiness of metal chips.
- Reduce the number of flutes. Excess in flutes tightens the space between cutting edges. It leads to stacking metal chips, which deteriorates cutting tool life and machining quality. As a rule of thumb, three flutes are enough for aluminum machining.
- Do not increase production rates without justification. The typical mistake is speeding up the production rates by saving time on extra cuts.
If a CNC machine is forced to make less frequent but deep cuts, the life of tooling deteriorates rapidly. It also conceives metal chips that are harder to get rid of. Frequent, shallow passes work much better overall.
7. Some Common Questions and Solutions to Issues
1. How to Get Awesome Surface Finishes on Aluminum?
First, you should choose the type of finishing that suits the purposes of the component being manufactured. Typically, options are mechanical finishes, pretreatment, bright dipping, anodizing, liquid paint, powder coating, and sublimation.
Some of the finishing may not suit a particular aluminum component because they may not meet your specifications.
You should consider all the minor nuances that accompany every type of finishing. Pay attention to the sharpness of a cutting tool. It should not be dull, so always monitor the state of your CNC machine tooling. Choose the appropriate cutting tool geometry, which suits a particular CNC machine and a component being manufactured.
In case you have chosen the correct finishing, all that’s left is to conduct the process with all the safety precautions.
Pay attention to the sharpness of a cutting tool. It should not be dull, so always monitor the state of your CNC machine tooling. Another item is the burr sticky on the part, don’t forget to remove the burr in the process.
2. Why Does Aluminum Turn Brown When Milling?
Frequently, aluminum turns brown or even black when machined. The typical cause is oxidation, as aluminum is prone to reacting with the surroundings.
You should ensure that the metal is not exposed to extra moisture. Additionally, we recommend you replace the coolant. Cleaning machined parts with hot soapy water may also help to reduce the probability of oxidation.
3. What is Coating for Milling Aluminum?
A manufacturer may choose from several options to mill aluminum. First, it is uncoated tolling. It may still provide solid performance but can quickly deteriorate over time.
Then, it is gold-colored ZrN (Zirconium Nitride) tooling, which is considered non-expensive but enhances the properties of tooling significantly.
Finally, there are various titanium nitride (TiN) based coatings. Examples are titanium carbo-nitride (TiCN), titanium aluminum nitride (TiAIN), and others. They are better overall and offer to improve tooling with various extra features and properties. Such as wear, temperature, and oxidation resistance, improved sharpness or hardness, etc.
4. Should You Use Oil When Milling Aluminum?
The term “oil” in CNC machining refers to aluminum alloy cutting fluid, in a broad sense. It enhances the precision of cutting tools and improves the finishing outcomes.
Considering that the fluid is not expensive and significantly increases the quality of milling, you definitely should use it.
5. How Do You Fixture Mill Thin Wall Aluminum?
The significant concern associated with milling is that thin sheet metals would be cut through if milled. Common fixtures do not work well in this case, as they do not solve the problem.
If you do not want the surface of the worktable to be partly milled as well, you need to take precautions. Here are two tips:
- Support a sheet metal with a few more layers. So, they can be milled simultaneously. It may slightly deteriorate dimensions, but the thing is that you may use regular fixtures. And surfaces will not be cut. Then, just put the under milled workpiece on the top of the next stack, and you are good to go.
- Use MDF or plywood. Just fix a workpiece on a wooden block so it is milled instead of your precious surfaces. In a few attempts, you will know how many parts can be processed without changing a block. MDF is also an option, but it may reduce tool life, in case a cutting tool is not sustainable to abrasives.
- Use the tape. If the problem is to fix a part, just use double-sided tape to hold the part to a block of wood or raw aluminum.
6. How Thin Can Aluminum Be Machined?
Machining thin aluminum can be a challenging process, but with the right tools and techniques, it’s possible to produce high-quality parts with extremely thin walls. Using methods such as casting, fabrication, and CNC machining, aluminum parts can be created with walls as thin as 0.001 inches. Achieving this level of precision requires careful control of the machining process to prevent deformation and ensure the integrity of the final product.
7. What is the Easiest Aluminum to Machine?
One of the easiest aluminum alloys to machine is Aluminum 6061-T6. This alloy is widely recognized for its versatility and is often the standard grade offered by most manufacturing companies for CNC machining. Aluminum 6061-T6 is not only easy to machine but also highly adaptable, allowing for different heat treatments to enhance its properties further. Its excellent mechanical properties, combined with good corrosion resistance and a high strength-to-weight ratio, make it an ideal choice for a wide range of applications. Whether you are working on a small-scale project or industrial manufacturing, Aluminum 6061-T6 provides reliable performance and ease of machining.
8. Summary
In essence, you may consider yourself an expert in aluminum machining if you make it properly to the very end of the post.
As you know now, aluminum is a soft metal, which cannot be processed similarly to stainless steel or any other hard material. Luckily, there are various cutting tools and operations to make any design in an aluminum workpiece.
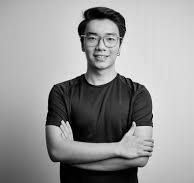
Lucas is a technical writer at ECOREPRAP. He has eight years of CNC programming and operating experience, including five-axis programming. He also spent three years in CNC engineering, quoting, design, and project management. Lucas holds an associate degree in mold design and has self-taught knowledge in materials science. He’s a lifelong learner who loves sharing his expertise.